Understanding Instrument Pipe Fittings: A Comprehensive Guide
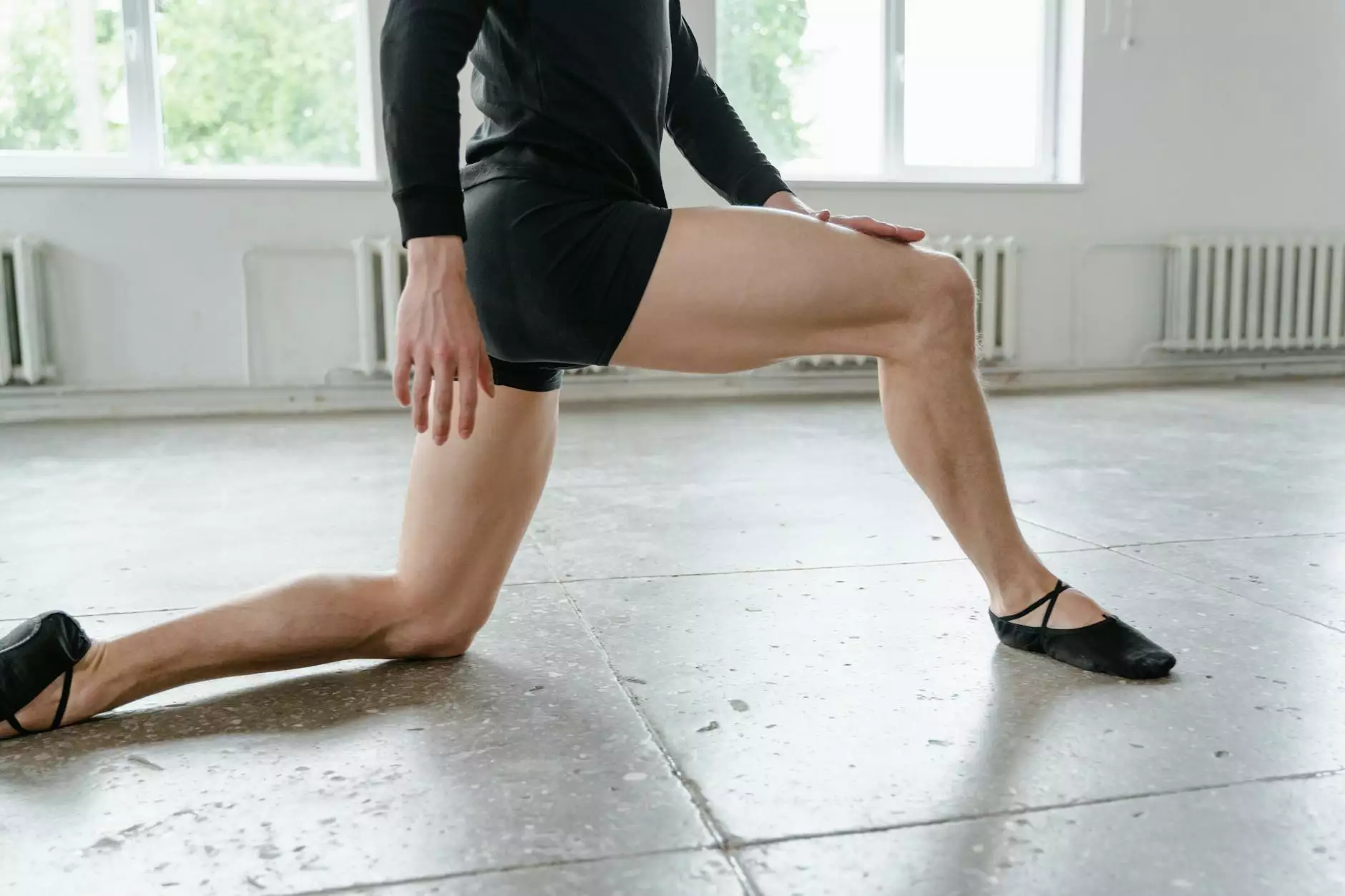
Instrument pipe fittings are critical components used in various industries for fluid and gas transfer systems. They ensure that connections between pipes, valves, and instruments are secure, leak-proof, and capable of handling high pressures and temperatures. In this article, we delve deep into the world of instrument pipe fittings, covering their types, applications, benefits, and how they can enhance the reliability of your business operations.
What are Instrument Pipe Fittings?
Instrument pipe fittings are specialized connectors that play a vital role in piping systems, especially in industries such as oil and gas, chemical manufacturing, and water treatment. Their primary purpose is to support fluid transfer by connecting various system components.
Key Characteristics of Instrument Pipe Fittings
- Material Quality: Typically made from stainless steel, brass, or plastic, these fittings provide excellent corrosion resistance.
- Pressure and Temperature Rating: They are designed to withstand high pressure and temperature fluctuations.
- Sealing Mechanisms: Many instrument fittings have advanced sealing technologies to prevent leaks.
Types of Instrument Pipe Fittings
Instrument pipe fittings can be categorized into various types based on their design and functionality. Here are some common types:
1. Elbow Fittings
Elbow fittings are used to change the direction of flow in a piping system. They come in various angles, such as 90 degrees and 45 degrees, allowing for efficient routing of pipes.
2. Tees
Tees are fittings that allow for the branching of a pipeline. They are vital for creating new piping routes or for connecting multiple branches to a main line.
3. Couplings
Couplings connect two pipes together, ensuring a smooth flow of fluids between them. They can be classified as regular couplings or reducing couplings, depending on the pipe sizes being joined.
4. Adapters
Adapters are fittings that facilitate the connection between two pipes with different diameters or threading types. They are essential in retrofitting existing systems.
5. Caps and Plugs
Caps and plugs are used to seal the ends of pipes or fittings. They prevent leaks and contamination in systems that are not in use.
Applications of Instrument Pipe Fittings
Instrument pipe fittings are prevalent in various industries due to their versatility and reliability. Here are some key applications:
1. Oil and Gas Industry
In the oil and gas sector, instrument pipe fittings are critical in connecting sensors, valves, and measurement tools. They help to monitor pipeline pressure, temperature, and flow rates.
2. Chemical Processing
These fittings are used to ensure secure connections in chemical plants, where fluids often flow under high pressure and aggressive conditions. The right fittings prevent leaks that could lead to hazardous situations.
3. Water Treatment Facilities
Instrument fittings play a crucial role in water treatment facilities, helping to connect filtration units, pumps, and measuring instruments to ensure clean water supply.
4. Power Generation
In power plants, instrument pipe fittings are utilized for steam and gas transfer systems. Their reliability is essential for the safety and efficiency of energy production operations.
Benefits of Using High-Quality Instrument Pipe Fittings
Choosing the right instrument pipe fittings can significantly impact the efficiency and safety of your operations. Below are some benefits of using high-quality fittings:
- Improved Safety: Quality fittings reduce the risk of leaks and failures, contributing to workplace safety.
- Increased Efficiency: Properly fitted connections enhance the overall efficiency of fluid transfer systems.
- Reduced Maintenance Costs: High-quality fittings require less maintenance and lower replacement frequency, saving costs in the long run.
- Customizability: Many manufacturers offer custom sizes and materials to fit specific business needs.
Factors to Consider When Choosing Instrument Pipe Fittings
Selecting the right instrument pipe fittings for your application is crucial for optimal performance. Consider the following factors:
1. Intended Use
Identify the nature of the fluids being transported (liquid or gas) and their chemical properties. This will influence the material and design of the fittings.
2. Pressure and Temperature Ratings
Ensure that the fittings can handle the maximum pressure and temperature of your system to prevent failures.
3. Threading Type
Choosing the correct threading type (e.g., NPT, BSPT) is essential for ensuring a leak-proof connection.
4. Compliance with Standards
Check if the fittings comply with industry standards and regulations to ensure safety and functionality.
5. Manufacturer Reputation
Opt for fittings from reputable manufacturers like FITSCH (fitsch.cn), known for their quality products and customer service.
Maintaining Instrument Pipe Fittings
To ensure longevity and optimal performance, regular maintenance of instrument pipe fittings is essential. Here are some tips:
1. Regular Inspections
Perform regular inspections of your piping system to identify any signs of wear, leaks, or corrosion. Early detection can prevent larger issues.
2. Clean All Fittings
Ensure that all fittings are regularly cleaned to prevent buildup that may affect performance. Follow the manufacturer's recommendations for cleaning methods.
3. Replace Worn Components
Replace any fittings that show significant wear or damage to maintain a safe and efficient system.
Conclusion
In summary, instrument pipe fittings are essential components that ensure the reliable operation of various industrial systems. By understanding the different types of fittings, their applications, and the benefits of using high-quality materials, businesses can enhance safety, efficiency, and overall performance. Make sure to partner with trusted suppliers like FITSCH to guarantee that you are using the best fittings for your specific needs. Quality in fittings not only secures the integrity of your system but also contributes significantly to the success of your operations.