Understanding Tooling Molds: A Gateway to Precision Manufacturing
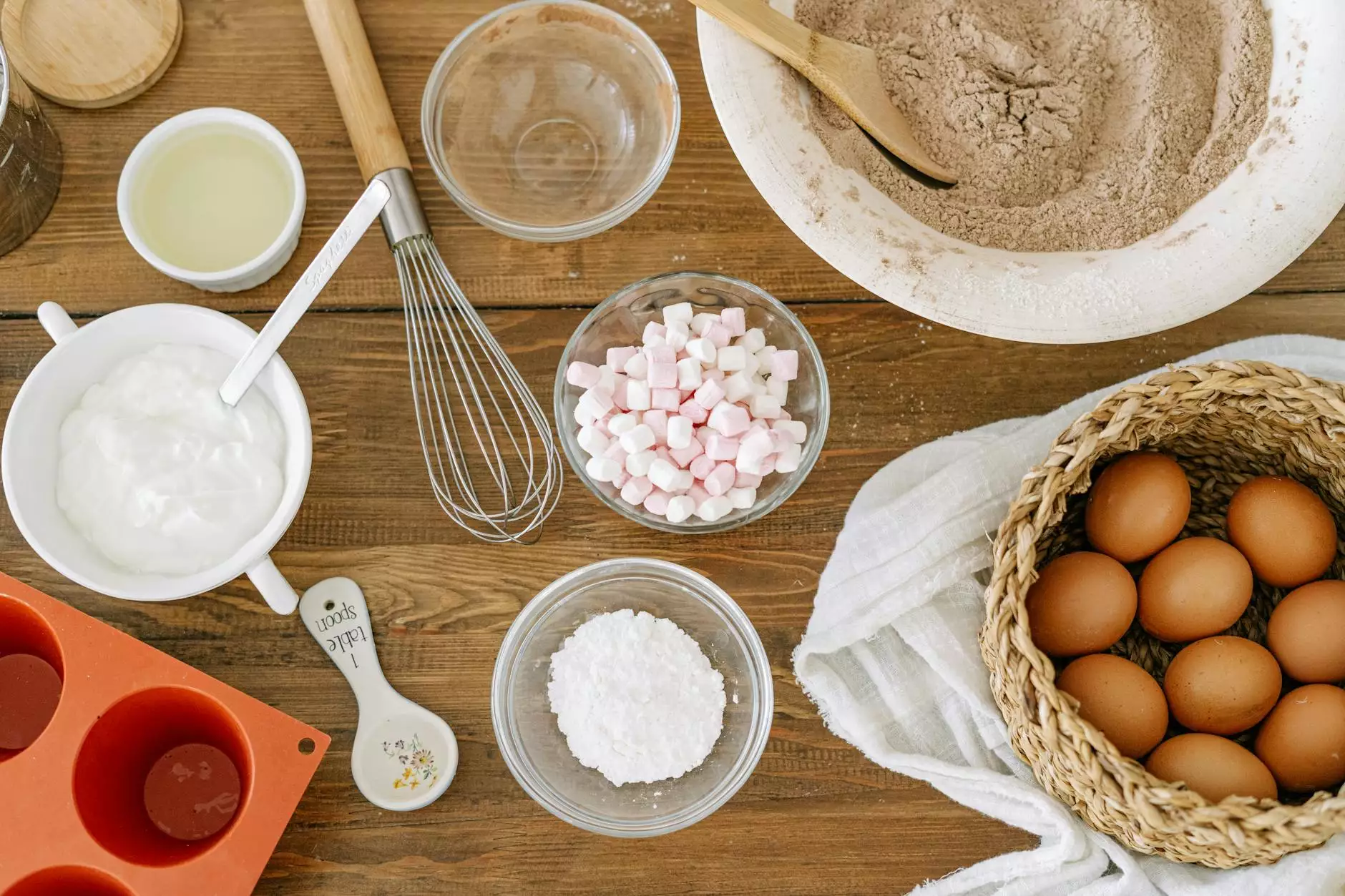
In the world of metal fabrication, the term tooling mold plays a pivotal role in achieving high precision and consistent results in production. This article delves into what tooling molds are, their applications, and their importance in the manufacturing process, with a particular emphasis on how renowned manufacturers like Deep Mould utilize them for superior outcomes.
What is a Tooling Mold?
A tooling mold is designed to shape and form materials into specific configurations during the manufacturing process. Typically made from durable materials such as steel or aluminum, tooling molds serve as the foundation for creating parts and products across various industries.
The Construction of Tooling Molds
Tooling molds are meticulously crafted through various processes including:
- Designing: Engineers create detailed designs using CAD software to ensure precision.
- Machining: The mold is then machined from solid blocks to create the desired shape.
- Finishing: Final finishing processes ensure that surfaces are smooth and free from imperfections.
The Importance of Tooling Molds in Manufacturing
Tooling molds are indispensable in the manufacturing sector for several reasons:
1. High Precision
When creating complex components, precision is key. Tooling molds allow for highly accurate reproduction of parts, minimizing errors and ensuring that every piece fits perfectly during assembly.
2. Cost Efficiency
While the initial investment in tooling molds may be significant, they lead to long-term savings by reducing the cost of errors, minimizing waste, and accelerating production speed.
3. Enhanced Productivity
With tooling molds, manufacturers can produce large volumes of parts quickly and consistently. This boosts productivity and allows companies to meet market demands effectively.
4. Versatility
Tooling molds can be used across a broad array of materials and industries, from automotive and aerospace to consumer products, showcasing their versatility in application.
Applications of Tooling Molds
The applications of tooling molds are vast and varied. Here are some key industries where tooling molds shine:
1. Automotive Industry
In automotive manufacturing, tooling molds are instrumental for producing parts such as bumpers, dashboards, and paneling. The precision offered by these molds ensures parts fit perfectly in vehicles, enhancing safety and performance.
2. Aerospace Sector
In aerospace, tooling molds are used for crafting lightweight yet strong components. Every piece must adhere to strict safety standards, making the precision of tooling molds a critical factor.
3. Consumer Goods
From household appliances to electronics, tooling molds help produce items that require complex shapes, ensuring high-quality finishes and enhancing consumer satisfaction.
Innovations in Tooling Mold Technology
With advancements in technology, tooling molds have evolved significantly:
1. 3D Printing
3D printing technologies are reshaping the way molds are made, allowing for quicker prototyping and customization. This innovation facilitates a rapid design process and the ability to easily modify existing molds.
2. Smart Manufacturing
Incorporating IoT and AI in the mold design and manufacturing process enhances monitoring and control, ensuring optimal conditions throughout production and allowing real-time adjustments to improve quality.
Choosing the Right Tooling Mold for Your Business
Selecting the appropriate tooling mold is crucial for successful production. Consider the following factors:
1. Material Requirements
Evaluate the material that will be processed through the mold. Different materials may require different types of molds to achieve optimal results.
2. Desired Output
Understand the production volume and complexity of the parts to determine which types of molds (e.g., single cavity vs. multi-cavity molds) would be most effective.
3. Budget Constraints
Evaluate both initial costs and long-term operational costs. Often, investing in higher quality molds pays off through increased efficiency and reduced waste.
4. Supplier Expertise
Partnering with experienced suppliers like Deep Mould brings invaluable expertise to the table, ensuring quality and reliability in the tooling molds you choose.
Challenges in Tooling Mold Production
While tooling molds are essential, there are challenges in their production:
1. Design Complexity
Highly intricate designs can increase manufacturing time and cost. Finding the right balance between complexity and feasibility is essential.
2. Material Selection
Choosing the right material for the mold is critical. Certain materials may not withstand the rigors of production, leading to costly repairs or replacements.
3. Cost Management
While high-quality molds may be an upfront investment, effectively managing costs through efficient production planning can mitigate financial strain.
Conclusion
In summary, tooling molds are fundamental to precision manufacturing in the metal fabrication industry. Their ability to produce complex, accurate, and high-quality parts drives efficiency and productivity. As technology continues to advance, the potential for tooling molds expands, paving the way for innovations that further streamline production processes.
For businesses looking to excel in manufacturing, understanding and optimizing tooling molds, such as those offered by Deep Mould, is not just beneficial; it is essential for future growth and success. Adopting cutting-edge practices in tooling mold production can set a business apart in a competitive landscape, resulting in not only significant operational improvements but also enhanced reputation and profitability.